Your Shopping Cart
Recovery boiler energy efficiency improvements
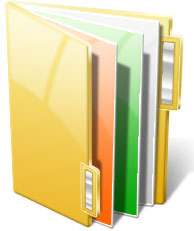
Format: PDF
Language: English
Product Type: Digital
Provider: TAPPI
Shipping: Available for download - Link will be provided in My ComplianceOnline section
Language: English
Product Type: Digital
Provider: TAPPI
Shipping: Available for download - Link will be provided in My ComplianceOnline section
Price:
$49.00
Product Details
Opportunities are identified for improving the net steam and power generation from a recovery boiler. These opportunities include factors both internal (steam generation and consumption) and external (liquor properties) to the recovery boiler operation.
Savings estimates are based on a boiler with an MCR (maximum continuous rating) steam capacity of 250 tonne/hr (550,000 lb/hr), with an exit wet-O2 level of 2.5% and a percent liquor solids of 75%. Using a steam value of $15/tonne ($6.8/1000 lb) for high pressure steam (from the recovery boiler or power boiler at the facility) at 100 bar (1500 psig), $10/tonne ($4.5/1000 lb) for medium pressure steam at 10-15 bar (150-200 psig) and $7/tonne ($3.0/1000 lb) for low pressure steam at 4-5 bar (50-75 psig). These are typical steam costs for a pulp mill burning natural gas at a cost of $5US per GJ (MMBTU) to make incremental steam. When determining the value of energy efficiency projects at a particular mill it is vital to develop these costs estimates specific for the mill being examined as these costs can vary greatly.
When discussing improvements, the term percentage points (increase/decrease) refers to an absolute change in a quantity (i.e. a 2 percentage point increase in as-fired solids would be an increase from 65% to 67%).
When using the term percent change, the change is as a fraction of the quantity (i.e. a 10% increase in the quantity of 50% would be to 1.10*50 = 55%).
You Recently Viewed